Conti LoadSense monitors a load’s center of gravity on the belt, as well as load distribution along the entire conveyor length, 24/7. Photo: Continental
Manufacturers specializing in conveying and material handling showcased their latest equipment and technology at ConExpo-Con/Agg. Ripper Tooth For Excavator
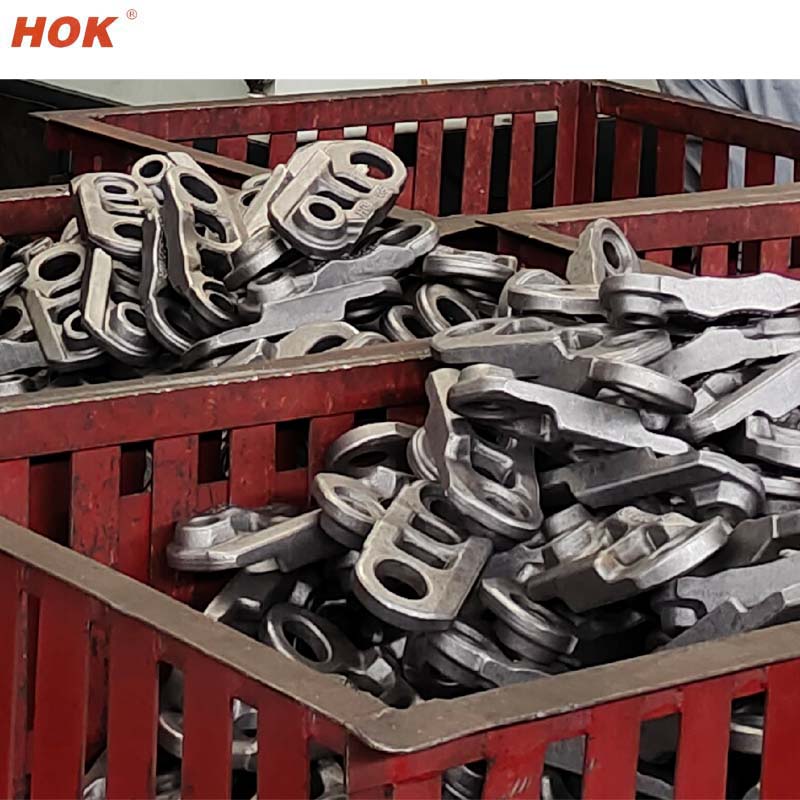
The developments introduced on the trade show floor position aggregate producers to improve their conveying system efficiency, maximize uptime and enhance safety at their operations. Here’s a look at some of the products introduced in Las Vegas:
Continental promoted several technologies at ConExpo-Con/Agg, including the Conti ConveyorInspect drone system, the Conti LoadSense monitoring system and Conti SurfaceProtect.
According to Continental, Conti ConveyorInspect allows operators to easily know the condition of belts and idlers, quickly locate the exact position of failing idlers, and track changes in rotating components over time. With real-time reporting, Continental says operators can better estimate their system’s component life and plan maintenance.
The Conti LoadSense monitoring system, meanwhile, combines radio wave detection and ranging with ultrasonic sensors to calculate the volume and position of the material conveyed on belts. The system scans material and the conveyor belt from different angles to determine the position of the load and the belt.
“Having this real-time monitoring allows operators of stone, sand or gravel quarries to measurably increase productivity,” says Patrick Raffler, who is responsible for digital solutions for the conveying industry at Continental.
The laser-based Conti SurfaceProtect is yet another conveying solution from Continental. The system continuously monitors the surface of flat fabric or steel cord conveyor belts in industrial and mining applications.
According to Continental, Conti SurfaceProtect automatically and continuously scans for damage to belts to reduce the risk of catastrophic belt failure. Conti SurfaceProtect evaluates belts for cuts, gouges or large impact damage events, as well as surface adhesion issues. Data is continually analyzed and reported, alerting operators to the exact position and size of any damage, the company says.
Flexco’s Travis Vliem offered a look at the Flexco Elevate dashboard at ConExpo-Con/Agg. Photo: P&Q Staff
Flexco, another manufacturer specializing in conveying and material handling, brought a unique technology to ConExpo-Con/Agg in Flexco Elevate Belt Conveyor Intelligence.
Flexco Elevate was created in partnership with Uptake, an industrial AI and IoT data science provider, to reduce the need for onsite inspections and allow operations to access real-time insights remotely from a dashboard. Flexco says those who utilize Flexco Elevate can quickly address belt conveyor performance issues and minimize unexpected downtime.
“In and of itself, it can tell you what’s happening from a wear perspective on the actual cleaner,” says Travis Vliem, digital product manager at Flexco Elevate.
According to Flexco, insights are captured through Elevate i3 devices that are attached to the ends of each Flexco belt cleaner. Information is wirelessly transferred to a dashboard, where producers can access information about the cleaners being utilized throughout their operation.
“Our business is making sure customers have productivity, and we want to be the partners in that productivity,” Vliem says. “This is a really good way for them to accomplish that.”
As Vliem describes, the Flexco Elevate system presents producers with a variety of opportunities to gain operational efficiencies. Belt cleaners are often a neglected piece of equipment, he says, so having real-time insights about them can allow maintenance personnel to focus on more pressing areas.
“If [the belt cleaner] is an asset that is in a good condition and there’s not a tension issue or a blade life issue, there’s not a need for a person to go and look at it,” Vliem says. “Focus that effort where the effort may need to be. If you have a different piece of equipment that’s having some issues, that person can deal with that quicker.”
The modular skirting system from Superior Industries is available in 5-ft. sections for conveyor belt widths up to 72 in. Photo: Superior Industries
Superior Industries also showcased its latest conveying solutions at ConExpo-Con/Agg, including updates to Exterra belt cleaners.
According to Superior, a new fast-acting click tensioner is available for the primary and secondary Exterra models. After installation, operators twist the tensioning unit a prescribed number of times to set the proper force. Click-count instructions are labeled on the aluminum housing protecting the springs.
Additionally, Superior touted conveyor components such as Titanium idler bearing seals and a modular skirting system. Superior says the new idler bearing seals offer superior performance in dusty, gritty applications. The modular skirting system is a solution for operations looking to manage dust.
“The dust containment system is for our conveyors and any other conveyors – it retrofits to other conveyors,” says Corey Poppe, the marketing communications manager at Superior.
Separately, Douglas Manufacturing Co. showcased a pair of new components at ConExpo-Con/Agg, including the Interceptor super-duty, self-cleaning magnetic separator and the Premier duty drum pulley.
According to Douglas, the Interceptor is specifically designed for portable plants. Features of it are a compact and lightweight design, a lagged drive pulley, a low-profile drive and Slide Tube take-ups.
The new Premier duty drum pulley, meanwhile, features thick rims and integral end discs. The result is a significantly longer service life, Douglas says.
Another pulley – the Wear Wolf wing model from Luff Industries – was also on display at ConExpo-Con/Agg.
According to Luff, the Wear Wolf features an abrasive chromium carbide overlay plate that provides extreme wear characteristics and replaces AR plates or hard surface welds. The overlay plate provides four to five times the life of mild steel, the company adds.
“It’s a product that has been around for a few years but has never been used in this application,” says Matthew Fasoli, CEO of Luff. “We had to modify the input in order to get it to work in conjunction with our product. It was driven 100 percent from customers saying: ‘Can we have something that doesn’t wear out?’”
If you enjoyed this article, subscribe to Pit & Quarry to receive more articles just like it.

Tractor Auger Attachment © 2023 North Coast Media LLC, All Rights Reserved.